Gear mold laser surface strengthening technology refers to the use of high-energy density laser beams and coatings, or cladding materials to treat the surface of gears or molds in a numerically controlled environment to change the structure or composition of the surface layer to achieve surface phase change strengthening or Enhanced repair techniques.
1. Metal Materials Science of Laser Phase Transformation Strengthening
The so-called laser phase transformation strengthening is to scan the workpiece with a laser beam, so that the surface layer of the workpiece is rapidly heated to above the critical point of Ac3. When the heated layer is removed from the spot, the temperature instantly enters the martensite region or bainite due to the heat conduction of the workpiece matrix. In the region, martensitic transformation or bainite transformation occurs, and the transformation strengthening process is completed.
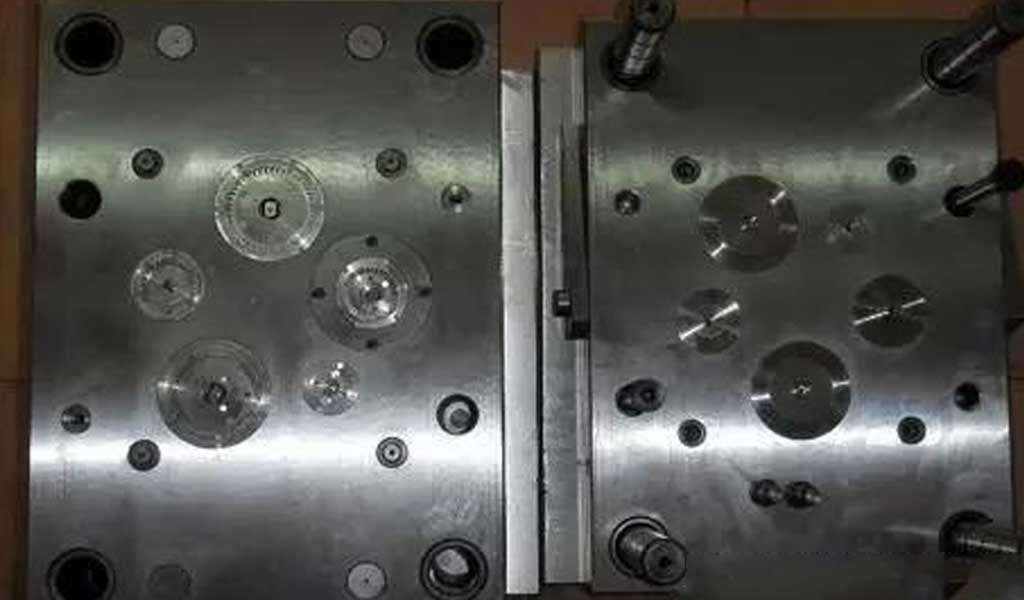
The phase change strengthening process has the advantages of good surface quality, and can control the hardness and the depth of the strengthening layer according to different materials, heat capacity of the workpiece, and different laser processing parameters. The technical factors that affect the strengthening effect in the traditional heat treatment process have changed a lot in the laser phase transformation strengthening.
1. Diffusion enhancement and distortion enhancement
Laser transformation strengthens to form austenite, and when laser irradiation is stopped, martensitic transformation occurs on the metal surface. The austenite formed in this process environment, whether it is the surface layer or the inner layer, has no chance for austenite grains to grow up.
The dispersed austenite grains form a dispersed martensite phase or bainite phase, which makes the structure have lattice strengthening and dispersion strengthening effect. Furthermore, the martensitic lattice formed under chilled conditions has a higher defect density than conventional quenching. At the same time, the retained austenite also obtains a very high dislocation density, so that the metal material has a distortion strengthening effect and the strength is greatly improved.
2. Non-oxidative decarburization quenching
In traditional heat treatment, if the workpiece is not protected during the heating process, oxidation and decarburization will occur, which will reduce the hardness, wear resistance, performance and service life of the workpiece.
The light-absorbing coatings used in laser phase change hardening have the properties of protecting the workpiece surface from oxidation.
3. Anti-fatigue mechanism of laser strengthening
One of the factors affecting the fatigue resistance of metal materials is the initiation time of fatigue cracks. Wear and fatigue promote each other in the process of material damage, and wear groove marks can become the initiation point of fatigue cracks, which accelerates the initiation of fatigue cracks.
The laser-enhanced layer has strong resistance to plastic deformation and adhesive wear.
4. Equally strong working layer
The cooling direction of conventional heat treatment is from the surface to the inside, the surface has the fastest cooling rate, and the cooling rate gradually decreases from the surface to the inside, so a gradient distribution of decreasing hardness values from the surface to the inside is obtained.
Although the heating direction of laser transformation strengthening is also the same, the surface temperature is high, and the heating time is relatively long, which can reach 0.2-0.25s, while the inner layer austenitization is completed in an instant, so that there is some austenite in the surface layer. Higher carbon concentration has stronger solid solution strengthening effect.
The cooling direction of laser quenching is opposite to that of conventional heat treatment. It is from the inside to the outside. Although the temperature of the inner layer is low, the cooling rate is the fastest. Although the temperature of the outer layer is high, it has the advantage of solid solution strengthening, but the cooling rate is the slowest. The concentration is slightly lower, but the distortion strengthening and dispersion strengthening are stronger, so that a nearly constant hardness value distribution is formed in the hardened layer.
The equal-strength working layer of the laser-enhanced parts avoids the phenomenon that once the surface of the conventional heat-treated parts is worn, the wear rate will be accelerated.
2. Gear Laser Phase Transformation Strengthening Technology
1. Material issues
The gear should be made of medium carbon steel, not low carbon steel. If low carbon steel is used, the matrix of the gear will have no strength guarantee, reducing the bending fatigue strength.
2. Original state
The best original state of the gear is the quenched and tempered state, which can be combined with the stress relief heat treatment after the forging of the gear blank. Forging blanks are normalized and tempered at high temperature to obtain the desired quenched and tempered state of the gear, which is a low-cost way.
3. Scanning method
The scanning methods of laser-strengthened gears mainly include circumferential continuous scanning and axial split-tooth scanning.
4. Pretreatment technology of gear laser strengthening
Appropriate pretreatment is one of the keys to ensure the laser processing of gears, and it has always been a difficult problem in laser processing. Reasonable and applicable pretreatment process can prevent quenching cracks on the gear surface, reduce the sensitivity of surface burnout, ensure the precision of the tooth surface after laser treatment, and increase the thickness of the hardened layer.
5. No lap technology and defocus difference problem
Due to the requirements of gear working conditions, the surface hardened layer of the gear needs to be reasonably distributed along the tooth profile, and the shape of the gear is special. In addition, the pitch circle surface of the gear cannot be overlapped with a quenched belt. Therefore, a special broadband focusing system is required.
In addition, since the irradiation of the tooth surface by the laser beam cannot ensure that different parts of the tooth surface have the same defocus amount, the selection of the irradiation position of the focus is the key link to ensure the reasonable distribution of the tooth surface hardness.
6. The performance of the laser gear
The performance of laser cutting gear is mainly in three aspects:
- Fatigue performance. If neither the laser gear nor the quenched and tempered gear is found to have broken teeth, it proves that it has high resistance to bending fatigue;
- Wear resistance;
- Serviceability.