Swiss Machining Aluminum
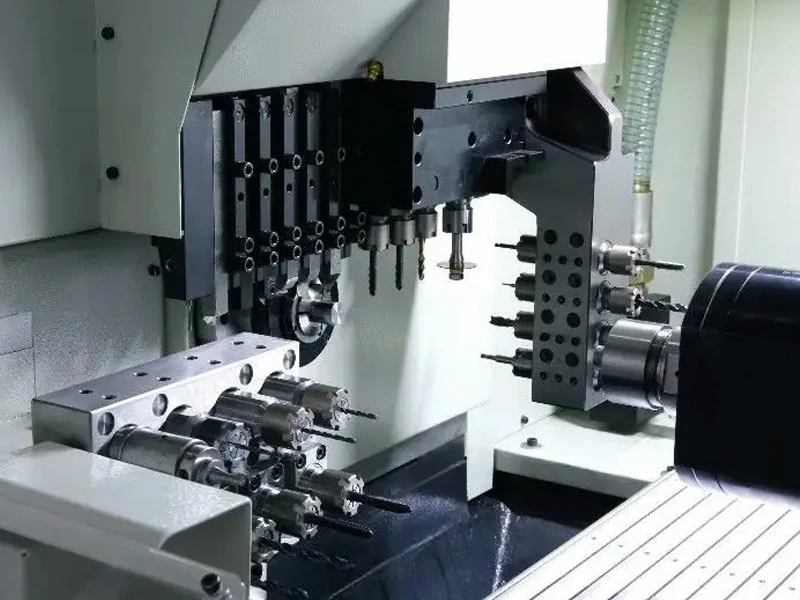
The full name of swiss machining is swiss type cnc machining, and it can also be called as a mobile headstock CNC automatic lathe, an economical turning-milling machine tool or a slitting lathe. Swiss machining was first used for precision machining of military equipment and watch parts. Later, with the continuous development of the industry, the market demand for aluminum swiss machining increased, and it was gradually applied to the cnc machining of civilian products.Swiss machine is a precision machining equipment, one-sided axis can realize three-axis linkage and four-axis linkage. Equipped with a B-axis Swiss machine, it can perform five-axis linkage composite machining, and can complete composite machining such as turning, milling, drilling, boring, tapping, punching, rolling and engraving in a single process. Loading and unloading batch production and cnc machining.
Swiss machining is suitable for precision machining of standard or special-shaped non-standard shafts such as precision hardware, aerospace, hydraulics, bearings, electronics, instrumentation, communications, auto parts, and medical equipment.
Aluminum CNC Swiss Machining Services – China Swiss Turning Parts Manufacturer
If you need intricate aluminum components fabricated by a reliable swiss turning parts manufacturer, you can trust with aluminum swiss CNC machining services offered at Be-cu, which is a China top swiss machining company that is specialized in swiss aluminum cnc services and precision hardware production for decades of years, and have the capability to provide CNC Swiss machining aluminum services with the latest Swiss turning and machining technology for the manufacturing needs of various industries all over the world. ISO 9001:2015 certified 3, 4, 5, 6 and 9-axis precision CNC Swiss machining services for aluminum and alumin alloy. Capable of handling parts up to 3/4 in. dia. capacity, 24 in. length and +/-0.0002 in. tight tolerance. With advanced Swiss lathe and Swiss machines, as well as other manufacturing facilities, our seasoned experts and technicians can give you the most cost-effective solutions and produce the highest quality aluminum swiss machined parts based on the industry standards and customer requirements.Our swiss cnc turning aluminum service ensures accuracy and speed,welcome to submit an inquiry online.
Get an instant online swiss cnc machining quote china estimation in seconds
- Direct quote from machine shops
- First-hand prices – no middleman
- Global payment protection
- Automatic ordering process
- Get quality parts as fast as 3 days
- Quality guaranteed parts no matter how complex they are
- Free DFM analysis by a dedicated engineer, before you make any payment
- Maximum machining diameters are 4 mm, 12 mm, 16 mm, 20 mm, 26 mm, 32 mm and 38 mm.
The Advantage Of Swiss Machining Aluminum
- Reduce product cnc machining procedures, shorten production takt time, and improve cnc machining efficiency. The swiss machine has the characteristics of reasonable structure, fast tool change and high reliability in design. It can realize the cnc machining requirements of previous multi-process procedures in one process, thereby shortening the production takt time. Make the product flow quickly in the production, greatly improve the production efficiency.
- Automatic production, high-precision cnc machining.The swiss machine is equipped with an automatic feeder to realize the fine grinding delivery of raw materials. After the product is changed and debugged, the cnc machining quantity can be set to realize automatic feeding, cnc machining and workpiece recovery. The matching gap between the raw material and the guide sleeve is adjusted to 0.005~0.010mm, which can stabilize the cnc machining and ensure the cnc machining accuracy. During the machining process between the spindle and the workpiece clamping part, the chip tool is always located at the proximal end of the guide sleeve, which ensures the cutting rigidity and provides a strong guarantee for constant machining accuracy.
- Reduce the investment of personnel and fixtures, and reduce the production cost. swiss machining can realize the operation of one person, and realize that one person can take care of multiple equipments, which reduces the investment of personnel. In addition, there is no need for tooling and fixture assistance during cnc machining, which reduces the cost of tooling and fixtures. A single swiss machine has the cnc machining capability of multiple equipments such as several turning and several milling in the past, which reduces the investment of other equipment and achieves the purpose of reducing production costs.
The Aluminum Types And Requirements Of Swiss Machining
The length of bars above 3mm diameter of swiss machine is concentrated in 2500~3200mm. The smaller the diameter, the shorter the bar length. Due to the limitation of straightness for 1-3mm diameter bars, the length of bars is concentrated in 1000-2000mm. The length of the aluminum tail material is mainly determined by the structure of the guide sleeve and the length of the product. The mechanical structure of the fixed guide bush and the floating guide bush is located 80-120mm forward from the limit position of the positive axis of the main shaft (take the swiss machining with a maximum machining diameter of 32mm as an example).
The aluminum material should not only meet the clamping length of the spindle, but also meet the supporting length of the guide sleeve. When it is not enough to meet the processing length of the last product, it will become tailings. The shorter the total length of aluminum, the more tailings are accumulated. Since there is no guide bush to support the machine without guide sleeve, only the spindle clamping length is required, and aluminum can be used to the maximum extent. The types of aluminum materials are mostly rods and wires, and the tolerance level requirements are IT7~IT9. Bar straightness is below 0.35mm per meter. The higher the tolerance of the diameter and the accuracy of the straightness, the higher the machining stability. Cylindrical materials are generally used for the shape of aluminum materials, and non-standard special-shaped materials can also be customized according to the requirements of product drawings, such as square or hexagonal materials, hollow materials, etc.
When using hollow material, the hole needs to be blocked on the tailing side to prevent the high pressure oil from flowing back to the feeder along the hollow hole when machining the inner hole, causing the cutting oil to overflow the machine tool. The spindle chuck and guide sleeve are consistent with the shape of the material. When the spindle processing product is a regular shaft shape, the back shaft chuck uses a common chuck or an extended chuck, and the groove shapes include three-lobed, four-lobed and S-slots. When metric material is selected for bar stock, the tolerance is the lower tolerance. When selecting the inch material, the tolerance is the upper and lower tolerance, and attention should be paid when selecting the spindle guide bush.
When using aluminum, it is necessary to ensure that the surface is clean and free of attachments. Both ends of the material are chamfered for guiding without interference when changing materials. When the equipment is changed and the specifications of the raw materials are changed, confirm that the diameter of the aluminum material matches the diameter of the feeder guide rail, shockproof sleeve, and telescopic tube to prevent the gap between the spare parts and the aluminum material from being too large during product processing. High-speed rotation produces abnormal noise or bumps the surface of the material, which will lead to bending and damage of the aluminum material, resulting in the scrapping of the workpiece and the suspension of processing. The gap between the floating guide bush and the material directly affects the dimensional accuracy and geometric tolerance of the product, so the aluminum material needs to be finely ground, which increases the unit cost of the aluminum material. Due to the difference between the equipment structure of Swiss machine and CNC lathe, the expression of the length of aluminum tailings is: length of aluminum tailings = support distance of the guide sleeve body + clamping length of the spindle chuck + the length of the last section smaller than the workpiece can be seen, when the batch is The accumulated cost of tailings during production is high.