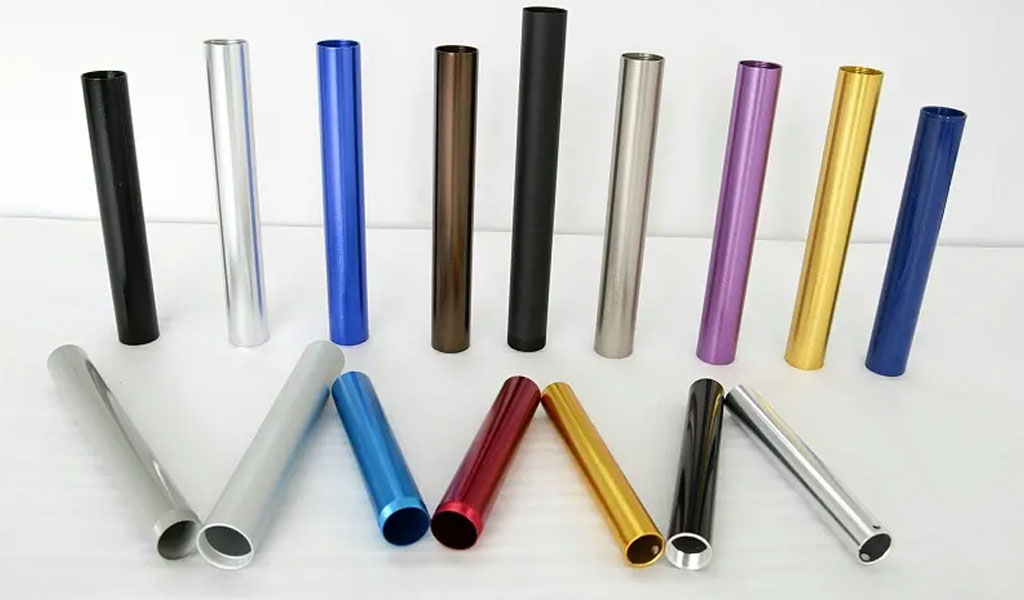
- At the cathode, H2 is released by the following reaction: 2H + + 2e → H2
- On the anode, 4OH – 4e → 2H2O + O2, the precipitated oxygen is not only molecular oxygen (O2), but also atomic oxygen (O), and ionic oxygen (O-2), which is usually represented by molecular oxygen in the reaction .
- The aluminum used as the anode is oxidized by the oxygen precipitated on it to form an anhydrous Al2O3 film: 2Al + 3[O] = Al2O3 + 1675.7KJ It should be pointed out that the generated oxygen does not all interact with the aluminum, and part of it is precipitated in the form of gas. .
- According to the current type, there are: direct current anodizing, alternating current anodizing, and pulse current anodizing which can shorten the cnc machining aluminum time to reach the required thickness, the film layer is thick, uniform and dense, and the corrosion resistance is significantly improved.
- According to the electrolyte, it is divided into: sulfuric acid, oxalic acid, chromic acid, mixed acid and natural color anodizing with organic sulfonic acid solution.
- According to the nature of the film, it is divided into: ordinary film, hard film (thick film), porcelain film, bright modification layer, semiconductor barrier layer and other anodization.
- The application of direct current sulfuric acid anodizing method is the most common, because it has anodizing treatment suitable for aluminum and most aluminum alloys; the film layer is thick, hard and wear-resistant, and better corrosion resistance can be obtained after sealing; The film layer is colorless and transparent, with strong adsorption capacity and easy to color; the processing voltage is low, and the power consumption is low; the processing process does not need to change the voltage cycle, which is conducive to continuous production and practical operation automation; sulfuric acid is less harmful to human body than chromic acid, and the supply is wide. , low price and other advantages.
The Anode Structure Of Aluminum
The Structure Of Anodized Film
The anodic oxide film consists of two layers, the outer layer is called the porous layer, which is thick, loose and porous, and has low resistance. The inner layer is called the barrier layer (also known as the active layer), which is thin, dense and high in resistance. A porous outer layer is grown on a dense inner layer with dielectric properties. In general, the film Anodizing Services is an array of hexagonal cylinders, each of which has a star-shaped hole filled with solution, shaped like a honeycomb structure, and the thickness of the pore wall is twice the pore diameter.- Barrier layer The barrier layer is composed of anhydrous AI2O3, which is thin and dense, has high hardness and prevents the passage of current.
- The porous outer oxide film is mainly composed of amorphous AI2O3 and a small amount of r-AI2O3.H2O also contains anions of the electrolyte.
The Properties And Applications Of Anodic Oxide Films
Anodized film has high hardness and wear resistance, strong adhesion, strong adsorption, good corrosion resistance and electrical insulation and high thermal insulation. Due to these specific properties, it has been widely used in various aspects. The main uses are:- Improve the wear resistance, corrosion resistance and weather resistance of parts.
- The transparent film produced by oxidation can be colored into various colored films.
- As a capacitor dielectric film.
- Improve the bonding force with the organic coating. As a coating base.
- For the bottom layer of electroplating and enamel.
- Other uses under development, solar absorption panels, ultra-high hardness films, dry lubricating films, catalyst films, nanowires, and deposition of magnetic alloys in porous films as memory elements.
The Closed Process Of closed Anodic Oxide Aluminum
The aluminum oxide film is a porous film, no matter whether it is colored or not, it must be sealed before being put into use, so as to improve its corrosion resistance and weather resistance. There are three types of treatment methods, namely high temperature hydration reaction blocking, inorganic salt blocking and organic matter blocking.
High Temperature Water Sealing
This method uses the hydration reaction of aluminum oxide film and water to change the amorphous film into a hydrated crystalline film: The hydration reaction can be carried out at room temperature and high temperature, but at high temperature, especially at the boiling point, the resulting hydrated crystalline film is a very stable and irreversible crystalline film. Therefore, the most commonly used sealing treatment of aluminum oxide film is boiling water. method or steam treatment.Inorganic Salt Sealing
The inorganic salt method can improve the fastness of organic coloring dyes, so it is commonly used in chemical coloring methods.- Acetate method
- Silica method
Organic Sealing Method
This is to immerse the aluminum oxide film with oil, paint or paint. Due to the high cost and increased technological process, it is not widely used. Most of the above two methods are used, and the first high temperature method is used. Hydration is the mainstream. Aluminum alloy sacrificial anode is suitable for cathodic protection of metal corrosion in ships, mechanical equipment, marine engineering and seaport facilities in seawater, as well as pipelines, cables and other facilities in sea mud.Be-cu aluminum machining china prototype company service include : aluminum cnc turning, aluminum milling service, aluminum extrusions, 5 axis machining aluminum, swiss machining aluminum, aluminum guide,aluminum products