Metal Finishing
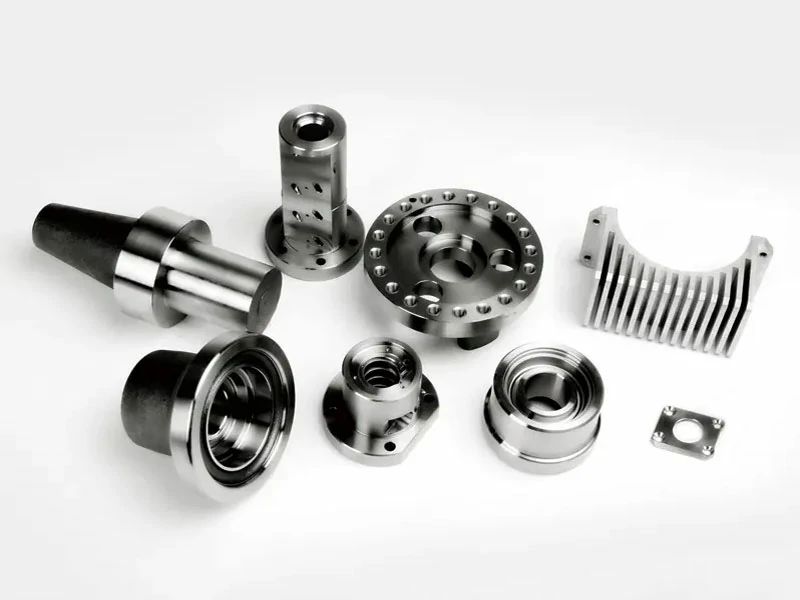
Different Types of Metal Finishes – Aluminum Parts Surface Finishing Services Available at Be-cu
Finishing serves two main purposes. That includes enhancing the final appearance. That means that a well-finished aluminum parts will look better than that which is not. Besides, a well-finished aluminum product will last longer because most finishes enhance anti corrosiveness. Here are some of the best finishes you can try out.
Powder coating
A solid powder is applied on top of the aluminum parts. This shields the aluminum from corrosive action among other wear and tear agents. This is done during the oven process as the machining aluminum is prepared for supply.
Sometimes, machining aluminum profiles are used in industries that involve emissions. Powder coating helps with compliance to meet the standards required. In these cases, the environment is a major conversation. For sustainability purposes, powder coating is used to keep the metal intact and minimize emissions to the environment.
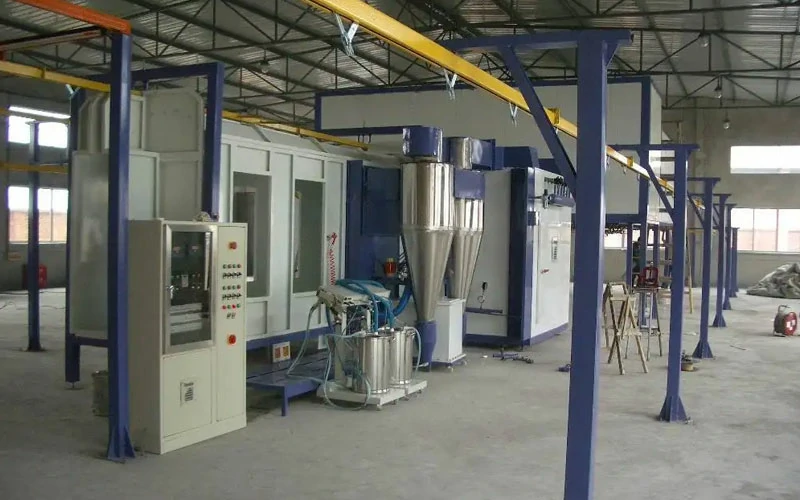
Anodizing
This is another popular finishing option utilized by aluminum machining companies. The electrochemical process offers increased surety by providing an additional shield to the aluminum surface. The benefit of anodization is that it accepts many metallic colors. Besides, all aluminum alloys can be anodized. This is a common finishing option for aluminum parts.

Sublimation woodgrain finish
Woodgrain effect is a special finishing option. In this type of finishing, woodgrain is put into a sublime film of art. This is a chance for the creatives to showcase their talent. Once the art has been drawn, sublimation allows the transfer of the art to the aluminum surface.
In most cases, sublimation is meant for aesthetic purposes. This type of finishing also has an impact on the longevity of the aluminum. That means it will last longer considering it’s shielded by another substance on top.
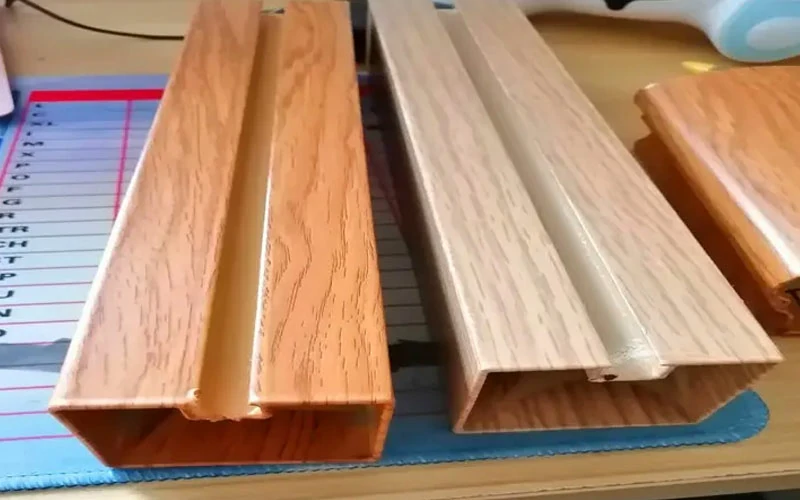
Mechanical finishes
This is also a good alternative. After buffing is done, the metal is either ground or sanded to give it a smooth or rough finishing depending on what the client wants or needs. Two things can be achieved by this. One, the aluminum machining is prepared for better aesthetic finishes. Or, it could be to enhance the surface quality of the aluminum product.
With better quality, the extruded aluminum becomes a better one. The client will therefore get better value for their money. The long-lasting aluminum parts will serve a lifetime and will only require repair, maintenance, or replacement of the aluminum product.
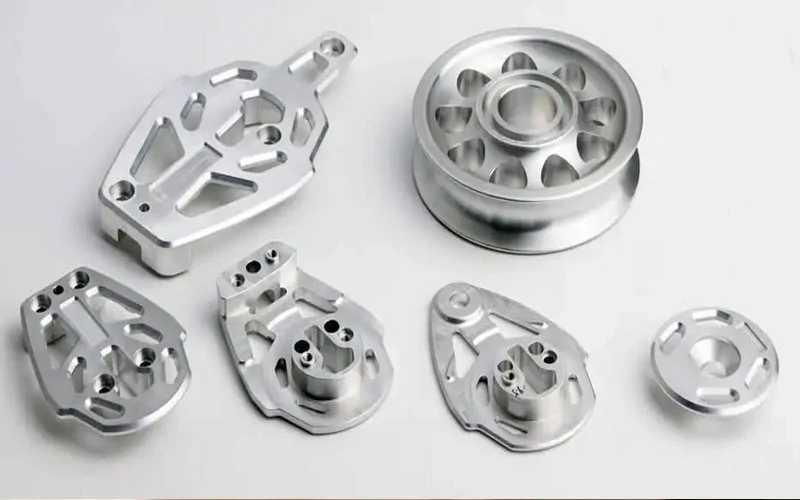
Liquid paintings
Most products are painted after production for aesthetic purposes. Different colors are applied to the aluminum parts. This provides a buffer against corrosion as well. For that reason, the aluminum profile products will last longer and cost less for maintenance.
A long-lasting aluminum machining ensures that the purpose is served well. For a while, the aluminum metal will be productive and efficient.

Polishing
Polishing, also known as buffing, a process of rubbing the surface of parts or utilizing a chemical action to produce a smooth and shiny surface, make the surface get significant specular reflection or reduce diffuse reflection in some materials.
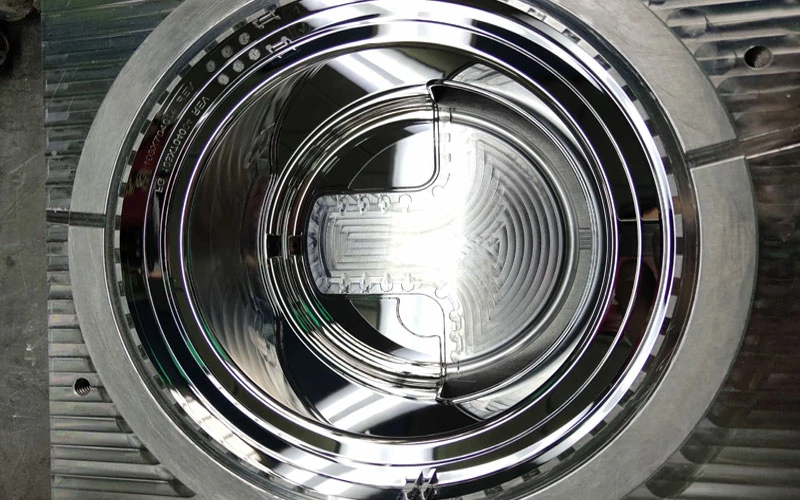
Heat Treatment
The process through utilizing heating or chilling usually under extreme temperatures to make the metal achieve a certain state or change some characteristics, heat treating techniques including annealing, tempering, hardening, precipitation strengthening, tempering, carburizing, normalizing and quenching.
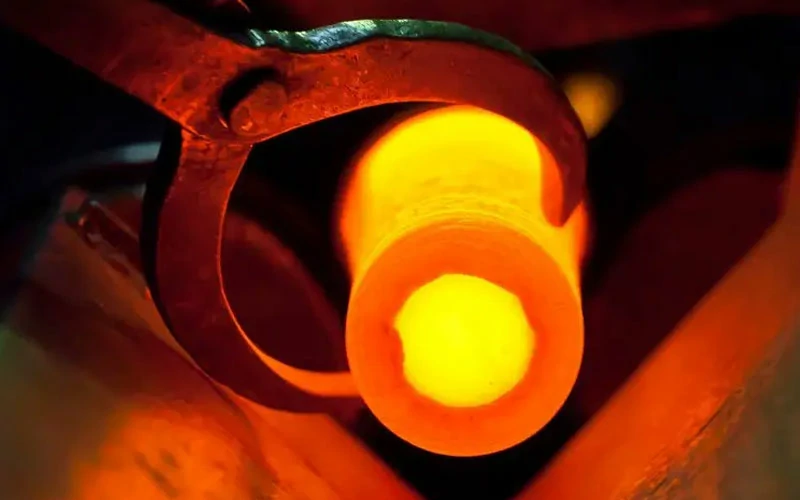
Black Oxide (Hot Blackening)
The technique also known as blackening, or gun bluing, a chemical process of forming a black conversion coating on stainless steel, copper and copper based alloys, zinc, powdered metals, silver solder, and ferrous materials, the black oxide coating can improve corrosion resistance and minimize light reflection

Passivation
A common chemical surface treatment method mostly for steel and stainless steel, to use a light coat of protective material to create a shell for enhancing the corrosion resistance or reducing the chemical reactivity. Passivation of stainless steel removes free ironand ferrous contaminants on metal surface with an acid solution to prevent rust.
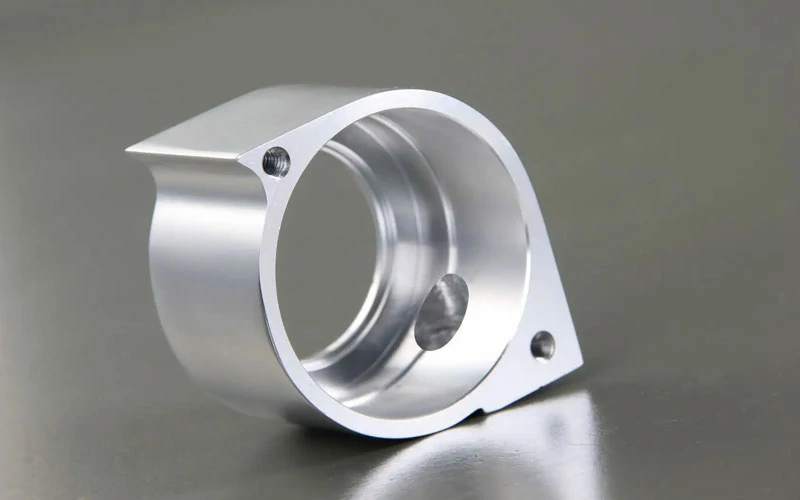
Abrasive blasting (Sandblasting)
The operation of propelling a stream of abrasive material composed of high-velocity sand-sizes particles against the metal surface under high pressure with blast equipment like air pressure system, to remove surface contaminants, clean metals or increase a texture, then change the smoothness or roughness of surface.
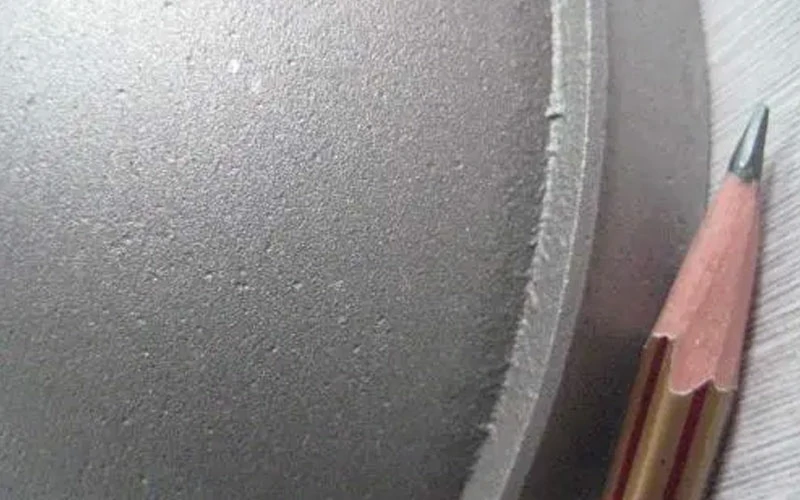
Electroplate

Other requirements or custom designs, welcome to contact us for a free quote fast!