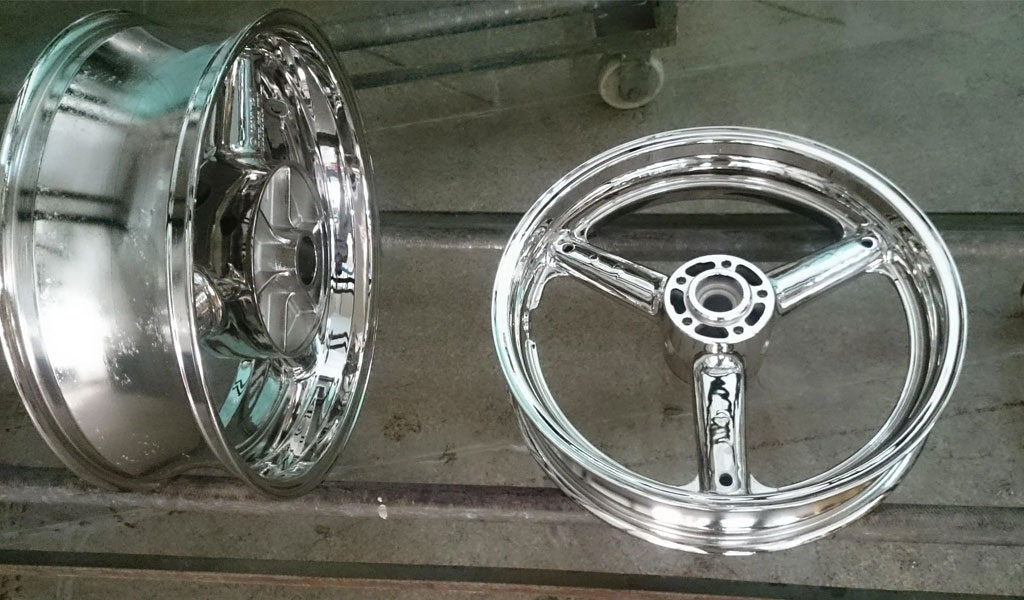
What Are The Advantages Of Aluminum Alloy Wheel Hub Compared With Steel Wheel Hub?
- Fuel economy. On average, each aluminum alloy wheel hub is 2kg lighter than the steel wheel hub of the same size, and a car can save 10kg with five. According to the Japanese experiment, every 1kg of weight reduction of a five seat car will save about 20L of gasoline a year. The research report published by the American Society of Automotive Engineers points out that although aluminum alloy wheels are more expensive than ordinary steel wheels, the fuel saved by each vehicle when it runs 20000 km is enough to cover the cost.
- Increase engine life. There is a negative correlation between engine load and engine life. The greater the load, the shorter the life. Because the aluminum alloy wheel hub is lighter than the steel wheel hub, it can prolong the service life of the engine.
- Good heat dissipation. The thermal conductivity of aluminum alloy is three times that of steel, and the heat dissipation effect is good. During long-distance high-speed driving, it can also keep the tire at an appropriate temperature, make the brake drum and tire not easy to age, increase the service life and reduce the chance of tire burst.
- High precision. The true circle accuracy of aluminum alloy wheel hub is up to 0.05mm, and the operation balance performance is good, which is conducive to eliminating the shaking of steering wheel.
- Strong and durable. The impact resistance, tension resistance and thermal strength of aluminum alloy hub are higher than those of steel hub. This is also one of the reasons why aluminum alloy plays an important role in national defense industry and aviation industry.
- Beautiful. Due to the limitation of production, the form of general steel wheel hub is monotonous and rigid, lack of change; Aluminum alloy wheels have various designs, plus good luster and color effect, which improves the value and beauty of the car.
The Production Technology Of Aluminum Alloy Wheel Hub
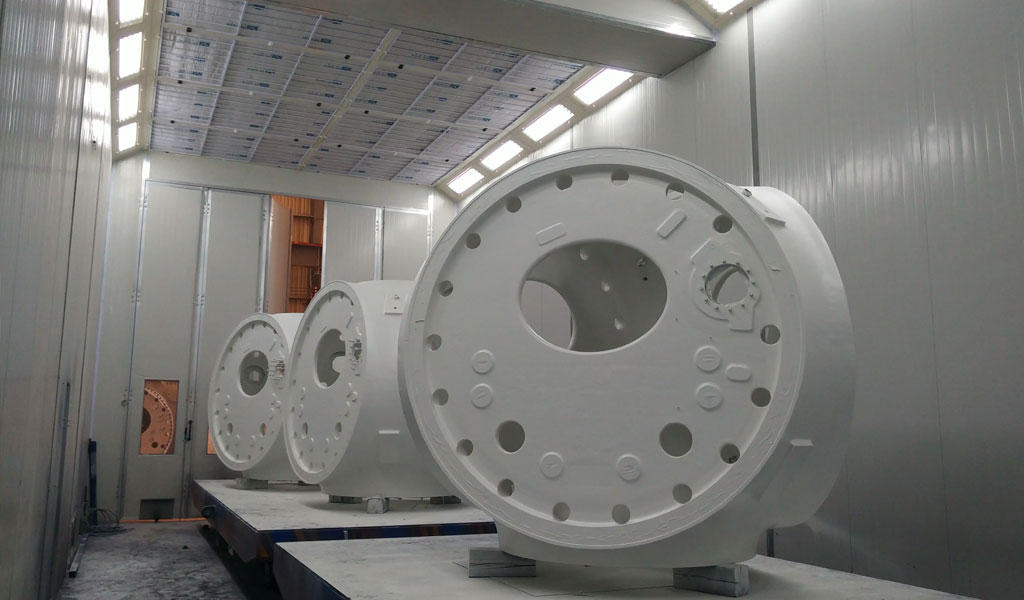
Wind power hub painting line
Gravity Casting For Wheel Hub
Metal mold gravity casting refers to a casting method in which liquid metal fills the metal mold by gravity under atmospheric pressure, which is also an ancient casting method. Because the liquid metal cools faster in the metal mold, the structure of the casting is denser than that of sand mold casting. This method has the advantages of simple process, high production efficiency, less equipment investment and low production cost. It is suitable for small and medium-sized production. However, the internal quality of the aluminum hub produced by this method is poor, the shrinkage cavity and porosity are serious, the inclusions such as oxide film and slag are easy to be involved in the casting during the pouring process, and sometimes the gas will be involved to form pore defects. At the same time, the yield of liquid metal is also low. Most vehicle manufacturers have rejected the wheels produced by this process, and there is a trend of gradual marginalization in the aluminum wheel hub manufacturing industry.Low Pressure Casting For Wheel Hub
Low pressure casting is to place the mold on a closed furnace, and a pipe (called liquid riser) is used under the mold cavity to communicate with the liquid metal in the furnace. If pressurized air is added to the metal level in the furnace, the liquid metal will flow into the cavity from the riser. After the liquid metal solidifies, release the compressed air in the furnace, and the non solidified metal flows back to the furnace from the liquid riser. By controlling the pressure and speed of the air flowing into the furnace, the speed and pressure of the metal flowing into the cavity can be controlled, and the metal can crystallize and solidify under pressure. This process is characterized by the crystallization of castings under pressure, dense structure, good mechanical properties and high metal utilization. Aluminum alloy casting technology Chinese is now quite mature in the Chinese mainland, and it is suitable for the production management of less humanized. It has been recognized by all the vehicle manufacturers as the mainstream technology of the Chinese mainland aluminum alloy wheel manufacturing industry, and its products are mainly sold to OEM and overseas retail market. For the aluminum alloy hub manufactured by low-pressure casting process, because the spokes are finally cooled and solidified, the spokes of some special shaped hubs are prone to quality problems such as shrinkage and looseness, while the strength of the rim is better due to the earliest crystallization.Squeeze Casting For Wheel Hub
Squeeze casting, also known as liquid die forging, is a new process integrating the characteristics of casting and forging. This process is to pour a certain amount of metal liquid directly into the open metal mold, act on the liquid metal with a certain pressure through the punch, make it fill, form, crystallize and solidify, and produce a certain amount of plastic deformation in the crystallization process. Squeeze casting has stable mold filling, no turbulence and uncoiled gas, and the metal crystallizes and solidifies directly under pressure. Therefore, the casting will not produce casting defects such as porosity, shrinkage and porosity, and has dense structure, fine grain and higher mechanical properties than low-pressure castings. The products not only have excellent mechanical properties close to forgings, but also have high efficiency and high precision of precision casting, and the investment is much lower than that of low-pressure casting. The disadvantage is that liquid die forging products, like traditional forging products, need milling to complete the modeling of spokes. A considerable part of automobile aluminum wheels in Japan have been produced by squeeze casting process. Toyota Motor Company has more than a dozen fully automatic squeeze casting equipment. Each equipment can produce an aluminum wheel hub in less than 2min. The whole process from pouring liquid metal to taking out the casting is controlled by computer, and the degree of automation is very high. China has also built a modern squeeze casting automobile aluminum alloy wheel hub factory in Guangdong. It has produced automobile aluminum wheels of various specifications and models. After identification, the product quality has reached the advanced level of similar foreign products. At present, countries all over the world regard squeeze casting as one of the directions of automobile aluminum hub production.Casting Spinning For Wheel Hub
Casting and spinning are divided into “low pressure casting + spinning” and “gravity casting + spinning”. At present, Korean car enterprises have a trend of fully adopting “low-pressure casting + spinning” for the forming process of aluminum wheel hub, and some products of other car systems also have demand for this process. This process is the mainstream process in the casting and spinning process, which is adopted by most enterprises making OEM products; At the same time, a small number of enterprises in overseas retail markets adopt the process of “gravity casting + spinning”. Theoretically, this process is feasible. It really combines the advantages of gravity casting and spinning, and the product quality has been improved. However, because the blank is produced by gravity casting process, the economy of this process is very poor and the production cost is very high. In short, because the spoke part of the cast rotary products is cast, it has the same advantages and disadvantages as the products produced by the casting process; The rim part is spun out, so the air tightness is good. In theory, the weight of spin casting products can be reduced, but the effect is not obvious in practical application.Conventional Forging For Wheel Hub
Forging is one of the earlier forming processes of aluminum wheel hub. Forged aluminum wheel hub has the advantages of high strength, good corrosion resistance, accurate size and small aluminum machining volume. Generally, its weight is only equivalent to 1 / 2 or less of the steel wheel with the same size. The fatigue strength and toughness of aluminum wheel hub are significantly better than that of forged wheel hub. At the same time, the performance has good reproducibility, and almost every hub has the same mechanical properties. The typical elongation of forged aluminum hub is 12% ~ 17%, so it can well absorb the vibration and stress of the road. Generally, the cast hub has a strong ability to withstand compressive force, but the ability to withstand impact, shear and tensile loads is far less than that of forged aluminum hub. Forged hubs have a higher strength to weight ratio. In addition, the surface of forged aluminum hub has no pores, so it has good surface treatment ability, which can not only ensure uniform coating, firm combination, but also good color. The biggest disadvantage of forged aluminum hub is that there are many production processes and the production cost is much higher than that of casting.The Casting Forging Method For Wheel Hub
It is a method of plastic machining of castings by using them as blanks in the forging process. Because forging is regarded as the final forming process of parts, it can eliminate casting defects, improve the organizational structure of products, and greatly improve the mechanical properties of products compared with castings. At the same time, it gives full play to the advantages of casting technology in forming complex parts, so as to reduce the forging process of products with complex shapes, greatly improve the utilization rate of materials and reduce the production cost. The properties of aluminum wheel hub produced by casting forging technology can fully meet the mechanical properties of forgings, but the production cost can be reduced by 30% compared with ordinary forgings. At present, since the process was successfully applied to mass production in September 1996, it has been adopted by many Japanese companies with good economic results. At present, only a few enterprises in the mainland (mainly Liuhe system in Taiwan) are using this process, and the equipment and technology come from Bulgaria.Semi Solid Die Forging Process For Wheel Hub
The so-called semi-solid die forging is a process that heats the semi-solid blank to a semi-solid state with about 50% volume liquid phase, and then forms a die forging to obtain the required finished parts close to the size. This is a new process between solid forming and liquid forming. Advantages of semi-solid die forging:- The shrinkage of parts in the die is small, which is easy to near final forming and reduces the amount of machining;
- The surface of semi-solid die forgings is flat and smooth, the internal structure is dense, the grain is fine, and the mechanical properties are higher than those of die-casting and squeeze casting;
- The forming is not easy to wrap air, and the macro pores and micro porosity are much less than those in conventional castings;
- Low forming temperature and long die life.
Forging Spinning For Wheel Hub
Compared with the high-end forming process, at present, only about 10% of domestic enterprises use this process for production, and the products are mainly supplied to the bus, truck and high-end car markets at home and abroad. The advantage is that the product has good internal quality, high product strength and light quality; The disadvantage is that the equipment cost is high, the spoke modeling of products manufactured by traditional forging process can only be completed by milling, the metal utilization rate is low and the production efficiency is not high. Forging is divided into traditional forging and rolling forging. Rolling forging can directly forge the shape of spokes.Be-cu aluminum machining china prototype company service include : aluminum cnc turning, aluminum milling service, aluminum extrusions, 5 axis machining aluminum, swiss machining aluminum, aluminum guide,aluminum products