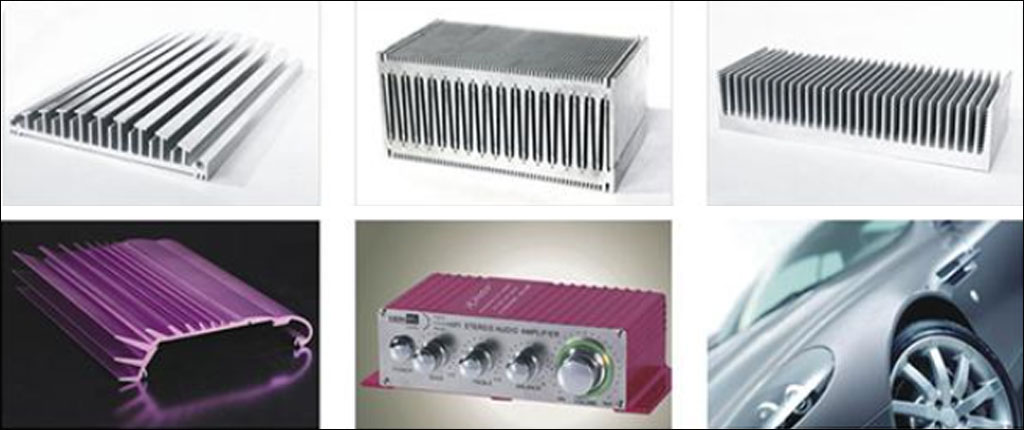
The Application of Aluminum Extrusion Heat Sink
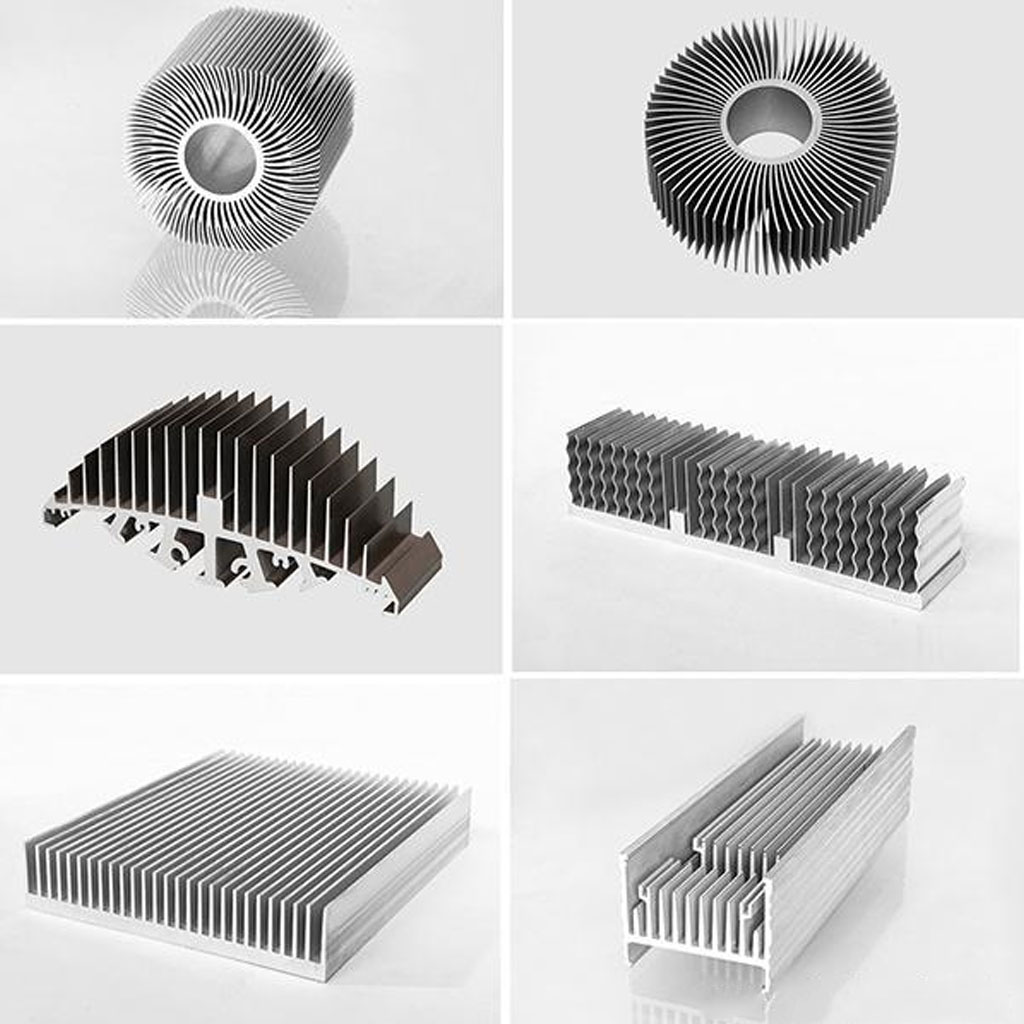
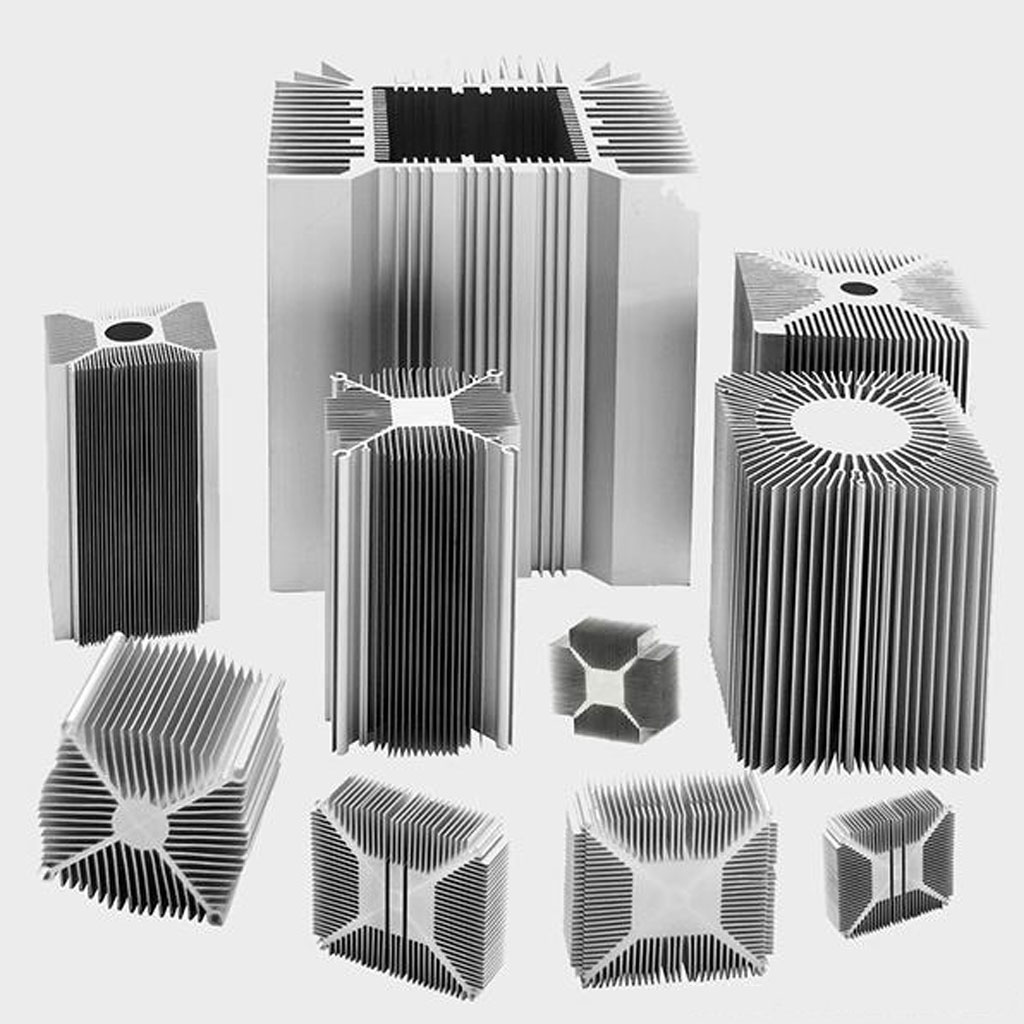
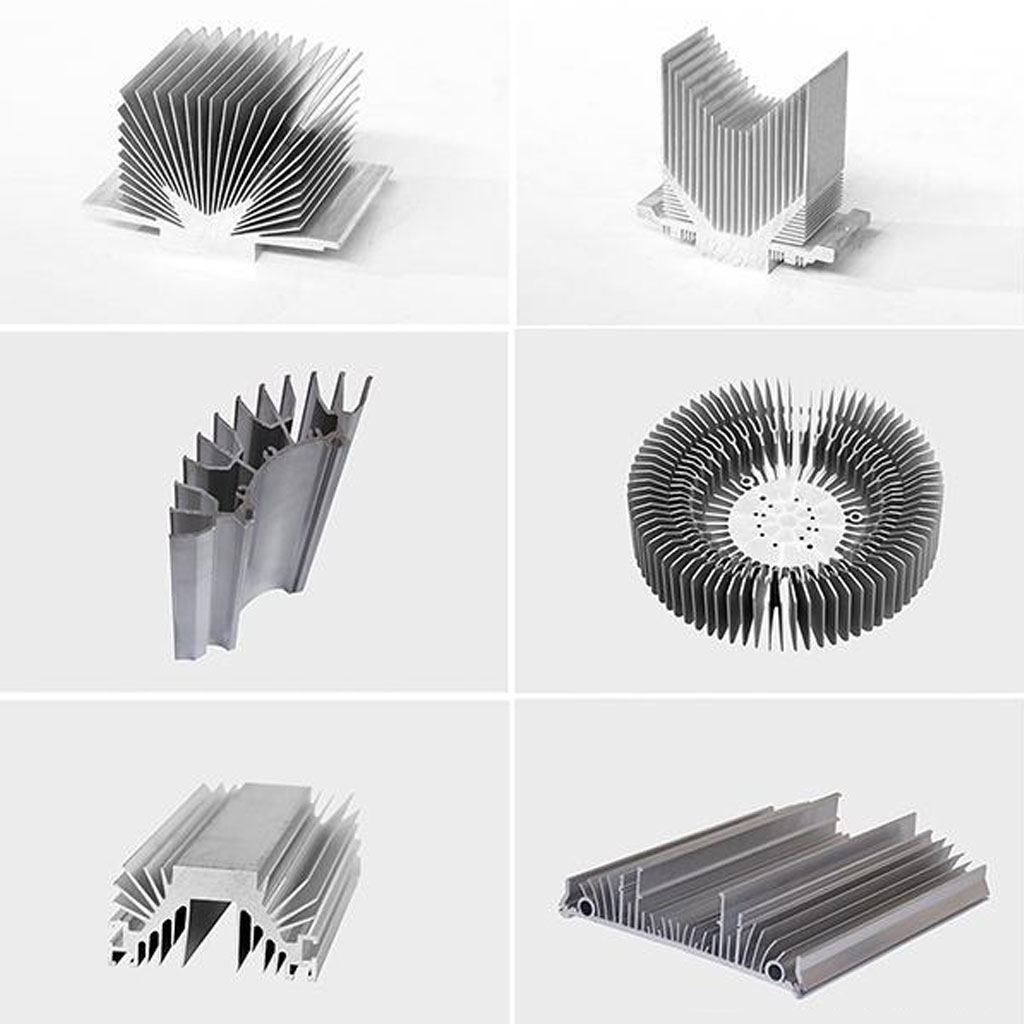
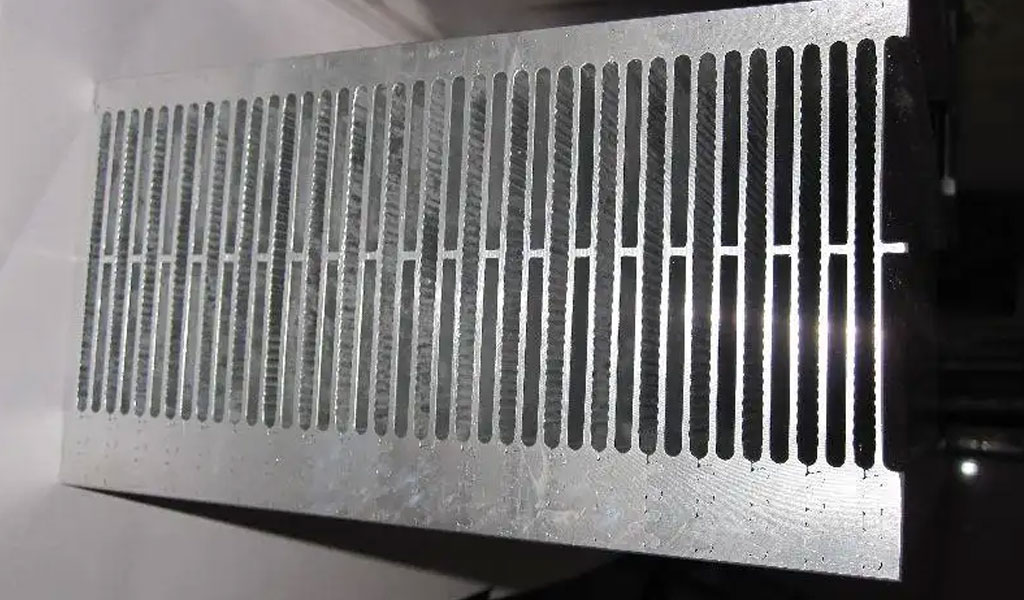
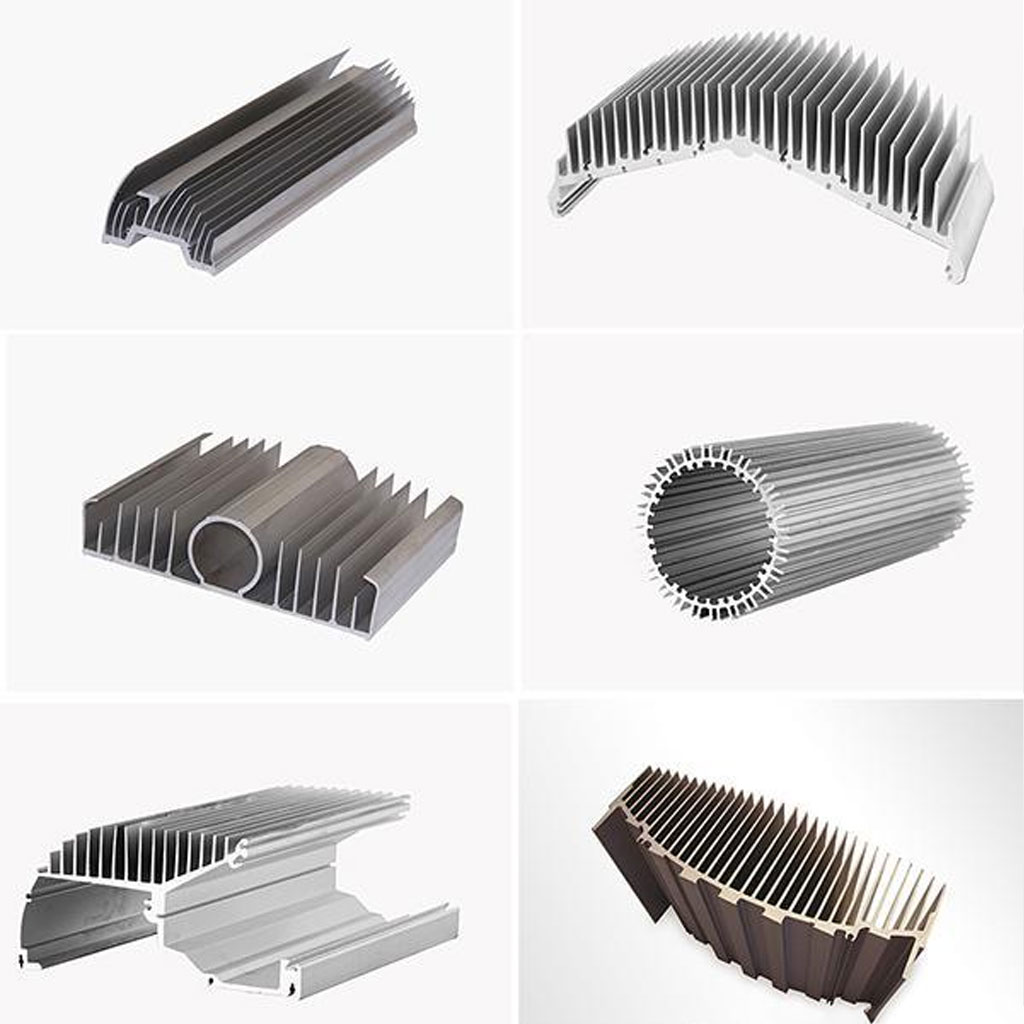
1. Quality Requirements Of Ingots
The alloy composition of the radiator aluminum ingot should be strictly controlled with the impurity content to ensure the purity of the alloy. For 6063 alloy, the content of Fe, Mg and Si should be controlled. The content of Fe should be less than 0.2%, the content of Mg and Si are generally controlled at the lower limit of the national standard, the content of Mg is 0.45%-0.55%, and the content of Si is 0.25%-0.35%. The ingot should be fully homogenized to make the structure and performance of the ingot uniform. The surface of the ingot should be smooth, no segregation tumor or sticky sand and mud is allowed. The end face of the ingot should be flat, and it should not be cut into steps or with too large a cut slope (the cut slope should be within 3mm). Because of the stepped shape or the inclination is too large, when extruding the aluminum profile of the radiator with a flat die, if the guide pin is not designed, the ingot directly touches the die. The stress is concentrated, and the tooth shape of the mold is easily broken, or the discharge sequence is different, and it is easy to cause the phenomenon of mold blocking or poor extrusion.2. Requirements For Aluminum Extrusion Molds
Because the molds of the radiator aluminum profiles are many slender teeth, they must bear a large extrusion force, and each tooth must have high strength and toughness. Those teeth with poor strength or toughness are prone to fracture. Therefore, the quality of mold steel must be reliable, and it is best to use H13 steel produced by reliable manufacturers, or choose high-quality imported steel. The heat treatment of the mold is very important. It should be quenched by vacuum heating. It is best to use high-pressure pure nitrogen quenching to ensure that the performance of each part of the mold is uniform after quenching. After quenching, three times of tempering are required to ensure that the hardness of the mold has sufficient toughness under the premise of HRC48-52. This is an important condition to prevent the broken teeth of the radiator aluminum profile die. The key to the successful extrusion of radiator aluminum profiles is that the design of the mold should be reasonable and the manufacturing should be accurate. Generally, try to avoid direct extrusion of the ingot onto the working belt of the die. For the flat and wide comb-shaped radiator aluminum profile, design a guide die with a smaller middle and larger sides to make the metal flow to both sides, reduce the extrusion force on the working belt of the die, and make the pressure distribution uniform. Due to the large difference in wall thickness of the aluminum profile section of the radiator, the difference should be maintained when designing the working belt of the mold. That is, the working belt should be particularly enlarged where the wall thickness is large, which can be as large as 20mm-30mm, and the position of the tooth tip To break out of the norm, keep the work belt to a minimum. In short, to ensure the uniformity of metal flow everywhere. For flat and wide radiator aluminum profiles, in order to ensure that the mold has a certain rigidity, the thickness of the mold should be appropriately increased. The thickness increase is about 30% – 60%. The production of the mold should also be very fine. The empty knife should be symmetrical up and down, left and right, and the middle. The machining error between the teeth should be less than 0.05mm. If the machining error is large, it is easy to produce skewed teeth, that is, the thickness of the heat sink is uneven. There may even be broken teeth. For a section with a relatively mature design, it is also a good method to use a mosaic alloy steel mold, because the alloy steel mold has good rigidity and wear resistance, and is not easy to deform, which is conducive to the forming of the radiator profile.3. Reduce The Aluminum Extrusion Force
In order to prevent the broken teeth of the radiator aluminum profile die, the extrusion force should be minimized, and the aluminum extrusion force is related to factors such as the length of the ingot, the size of the alloy deformation resistance, the state of the ingot, and the degree of deformation. Therefore, the cast rod for extruding the aluminum extrusion profile of the radiator should not be too long, which is about (0.6-0.85 times the length of the normal cast rod). Especially when trying out the mold and extruding the first cast rod, in order to ensure the smooth production of qualified products, it is better to use a shorter cast rod, that is, a cast rod with a normal cast rod length (0.4-0.6) times. Try out. For radiator aluminum profiles with complex shapes, in addition to shortening the length of the cast rod, pure aluminum short casting can also be considered for the first trial extrusion, and after the trial extrusion is successful, the normal ingot is used for extrusion production. Ingot homogenization annealing can not only make the structure and properties uniform, but also improve the extrusion performance and reduce the extrusion force, so the ingot must be homogenized annealing. As for the influence of the degree of deformation, since the cross-sectional area of the aluminum profile of the radiator is generally relatively large, and the extrusion coefficient is generally within 40, the influence is small.4. Aluminum Extrusion Process
The key to the production of radiator aluminum profiles is the first trial of the extrusion die. If conditions permit, you can first do a simulation test on the computer to see if the working belt of the die design is reasonable, and then try the die on the extrusion machine. The first mold test is very important. The operator should let the main plunger move forward and move slowly at a low pressure lower than 8MPa. It is best to have someone use a flashlight to look at the exit of the mold, and wait for every heat dissipation of the extrusion mold. After the sheets are evenly extruded into the die hole, the extrusion can be gradually accelerated and accelerated. When the radiator aluminum profile continues to be extruded after the mold test is successful, attention should be paid to controlling the extrusion speed to achieve smooth operation. When producing radiator aluminum profiles, attention should be paid to the heating temperature of the mold, so that the mold temperature is close to the ingot temperature. If the temperature difference is too large, due to the slow extrusion speed when pressing, the metal temperature will drop, and the phenomenon of mold blocking or uneven flow rate is easy to occur.The Surface Treatment And Painting Knowledge Of Extruded Aluminum Heatsink
The surface treatment of extruded aluminum radiator includes: metal electroplating, oxidation coloring, rubbing (embossing), sandblasting, polishing; three surface spraying processes are: spray primer, topcoat and finish paint and Secondary spray. The surface treatment of extruded aluminum radiator is to improve performance. The specific methods must be familiar with the correct operation. Common aluminum surface treatment methods are as follows:- Metal electroplating method: It is relatively common, and there is a process of electroplating after grinding.
- Oxidation (coloring): The use of aluminum surface treatment oxidation is divided into two aspects, which can enhance the physical properties and achieve the purpose of coloring.
- Rubbing pattern: there is called wire drawing, the performance is similar to the car pattern, all of which form a smooth continuous pattern on the surface, the difference is that the car pattern is a circular pattern, and the rubbing pattern is a straight line pattern.
- Sandblasting: The purpose of aluminum surface treatment is to overcome and cover up some defects of aluminum alloy in the machining process and to meet some special requirements of tempering furnace customers for product appearance. There are glass sand, tungsten sand, etc., showing different feelings, similar to the rough texture of frosted glass, and fine sand can also show high-end products.
- Polishing: Overcoming defects, deburring and brightening the surface.
- Car texture: Aluminum surface treatment is a treatment method for reprocessing after the mold is formed. The texture is processed by a lathe, and the overall performance is extremely regular texture characteristics.
- Pre-treatment process: degreasing and decontamination of aluminum material→water washing→alkali washing (degreasing)→water washing→pickling→water washing→chromization→water washing→pure water washing
- Spraying process: spray primer → topcoat → finish paint → baking (180-250 ℃) → quality inspection
- The purpose of pre-treatment: before the aluminum alloy profiles and plates are sprayed, the surface of the workpiece should undergo degreasing, decontamination and chemical treatment to produce a chromed film, increase the bonding force between the coating and the metal surface and the anti-oxidation ability, which is conducive to prolonging the paint The useful life of the membrane.
- Primer coating: As the primer coating of the closed substrate, its function is to improve the penetration resistance of the coating, enhance the protection of the substrate, stabilize the metal surface layer, and strengthen the adhesion between the topcoat and the metal surface, which can ensure the surface The color uniformity of the paint coating is generally 5-10 microns thick.
- Topcoat: The topcoat is the key layer of the spray coating. It provides the decorative color required by the aluminum material, makes the appearance of the aluminum material meet the design requirements, and protects the metal surface from the external environment atmosphere, acid rain, and pollution. , to prevent UV penetration. Greatly enhances the anti-aging ability. The top coat is the thickest layer of paint in spraying, and the thickness of the paint layer is generally 23-30 microns.
- Overcoat paint coating: Overcoat paint coating is also called varnish coating. The main purpose is to more effectively enhance the paint layer’s resistance to external erosion, protect the topcoat coating, increase the metallic luster of the topcoat color, and make the appearance more vivid. Dazzling, the coating thickness is generally 5-10 microns. The total thickness of the three-spray coating is generally 40-60 microns, and can be thickened if required.
- Curing treatment: The three-spray coating generally needs secondary curing. The aluminum material enters the curing furnace for treatment. The curing temperature is generally between 180 °C and 250 °C, and the curing time is 15-25 minutes. paint, providing optimum temperature and time. Some of the chlorocarbon annealing furnace fan spraying plants (curium oil plants) also have two curing treatments during the third spraying according to their own experience.
China Top Aluminum Extrusion Heat Sink Suppliers & Manufacturer
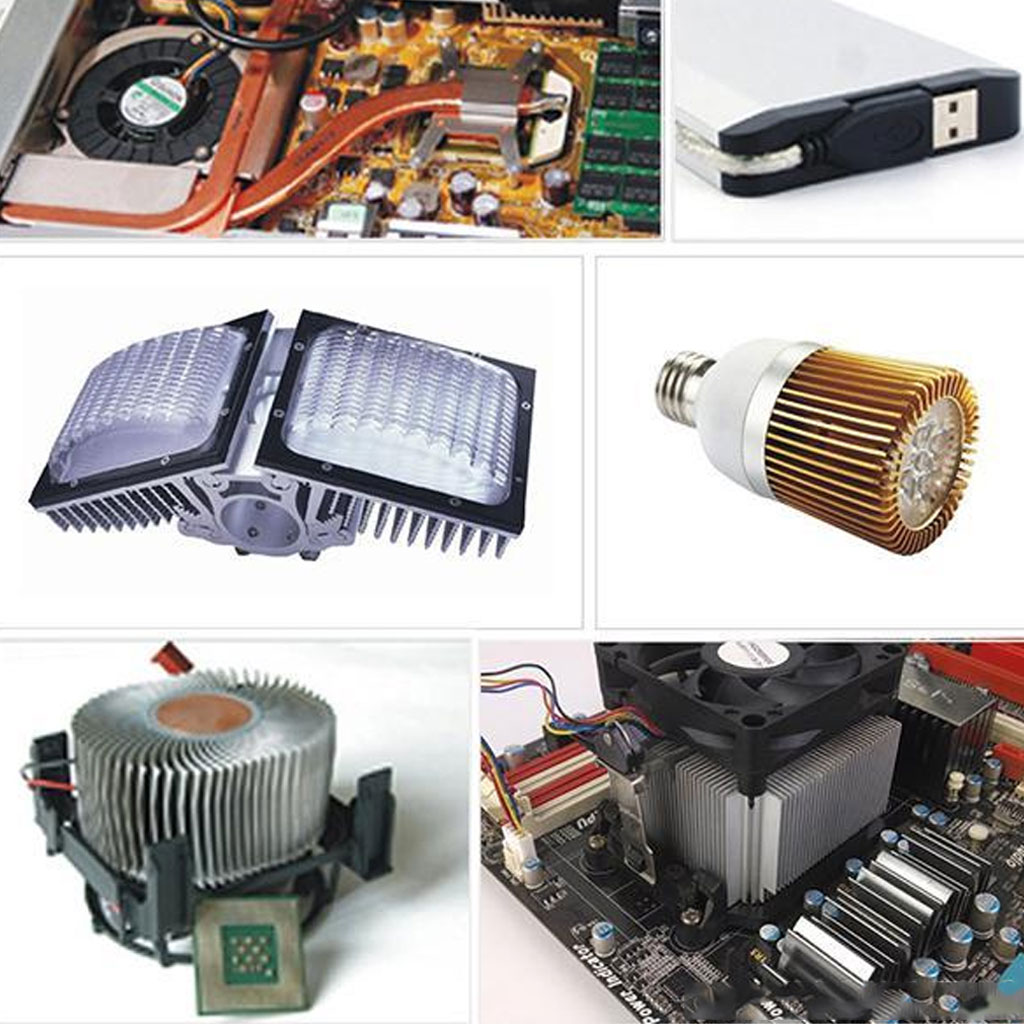
Be-cu aluminum machining china prototype company service include : aluminum cnc turning, aluminum milling service, aluminum extrusions, 5 axis machining aluminum, swiss machining aluminum, aluminum guide,aluminum products