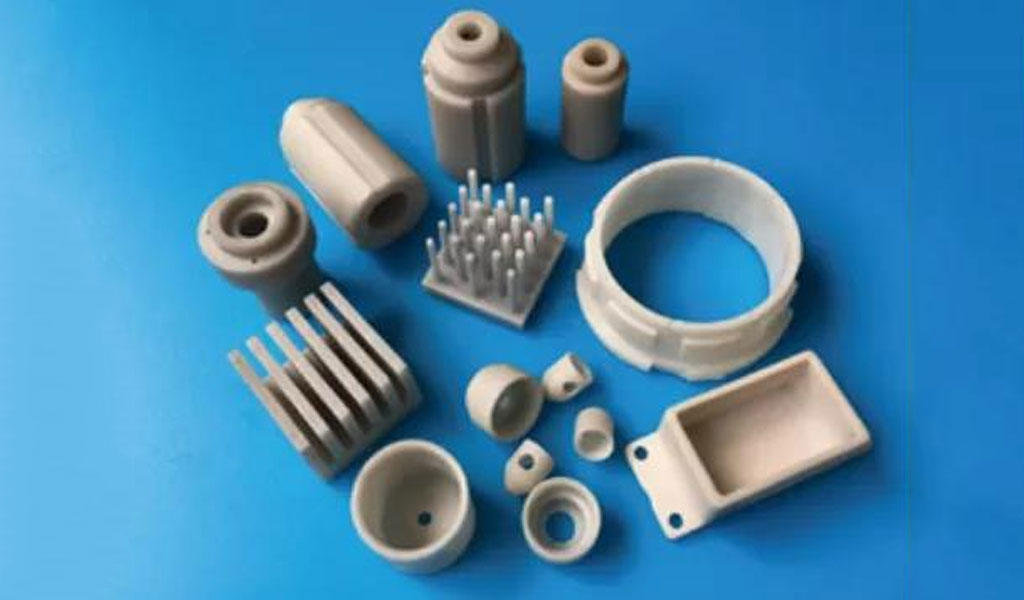
Main methods of metallization of aluminum nitride ceramics
To use aluminum nitride ceramics as electronic devices, it is often necessary to effectively connect with other materials (metals, alloys, etc.). In order to facilitate the connection, in many cases it is necessary to metallize it first. At present, there are many methods of metallization of aluminum nitride ceramics, mainly including thin film metallization (such as Ti/Pd/Au), thick film metallization (low temperature metallization, high temperature metallization), electroless metallization (such as Ni plating), direct metallization Bonded copper (DBC) metallization, active sealing, etc. The thin film metallization method uses vacuum coating methods such as sputtering coating to combine the film material and the substrate. Since it is vapor deposition, in principle, any metal can be formed into a film, and any substrate can be metallized, and the deposited metal layer is uniform and combined. high strength. However, the thin film metallization requires a subsequent patterning process to realize the pattern preparation of the metal leads, and the cost is relatively high. The thick film metallization method is to form a metal layer for sealing, a conductor (circuit wiring), a resistor, etc. on a ceramic substrate by screen printing, and form a brazing metal layer, circuits, and lead contacts by sintering. The advantages of the thick film method are good electrical conductivity, simple process, suitable for automation and multi-variety small batch production, but the bonding strength is not high, and it is greatly affected by temperature, and the bonding strength is very low at high temperature. The direct copper cladding method uses a high temperature melting and diffusion process to clad the ceramic machining substrate and high-purity oxygen-free copper together. The formed metal layer has good thermal conductivity, high adhesion strength, excellent mechanical properties, easy etching, insulation and thermal cycling. The advantage of high capacity, but the subsequent patterning process is also required, and the oxide layer formed during the surface heat treatment of AlN will reduce the thermal conductivity of the AlN substrate.Aluminum nitride ceramic laser metallization
Among the above-mentioned common metallization methods, the process flow of thin film metallization, electroless metallization method, and direct copper cladding method is relatively complicated, and involves patterning process, which increases the production cycle and production cost. Although the thick film metallization process is simple, the bonding strength is not high and it is easily affected by temperature. In order to solve the above problems, in recent years, the laser metallization method has gradually become one of the research hotspots. Laser metallization utilizes the thermal effect of laser to thermally decompose the surface of AlN to directly generate a metal conductive layer. It has the advantages of low cost, high efficiency, and simple equipment maintenance, and has been widely used in production practice.1. Principle of aluminum nitride laser metallization
The mechanism of using a laser to achieve metallization of aluminum nitride is to thermally decompose aluminum nitride using the high temperature generated by the laser. Aluminum nitride can be decomposed into metal aluminum and nitrogen when heated. But at different temperatures, the aluminum and nitrogen produced by the decomposition are in different forms. When the laser energy is very high, the aluminum nitride is decomposed into aluminum vapor and nitrogen atoms. As the energy decreases, the aluminum nitride does not undergo a decomposition reaction, and changes from solid state to gaseous evaporation. The energy is further reduced, and aluminum nitride decomposes into aluminum vapor and nitrogen atoms. Nitrogen, none of the reactions in these cases can achieve metallization of aluminum nitride. To form a metal aluminum layer on the surface of aluminum nitride, an appropriate energy density should be selected to cause reaction (4) to decompose the aluminum nitride into solid aluminum and nitrogen gas to form a conductive aluminum layer on the surface of the aluminum nitride.2. Factors affecting laser metallization
- At present, lasers in the two wavelength ranges of ultraviolet and infrared are mainly used in the research of laser metallization of aluminum nitride. Metallization using an infrared laser. Compared with ultraviolet laser, infrared laser has higher transmittance to aluminum nitride and stronger thermal effect, which can decompose deeper aluminum nitride, so that infrared laser can produce thicker metal layer.
- In the process of laser metallization of AlN, the same laser will have a great influence on the metallization effect when the process parameters change. The main process parameters are energy density, pulse width, and spot overlap rate. Explore the appropriate laser process parameters to get better AlN metallization effect is necessary. The energy density slightly lower than the ablation threshold is selected to ensure that a thick and dense metal layer can be formed without ablation; the thermal effect of the laser is positively related to the pulse width, so choosing a large pulse width is conducive to the thermal decomposition of aluminum nitride; The connection rate is around 96%.
- The flat top beam can be used to produce a uniform and dense metal layer, and there is no high requirement for the spot overlap ratio, which avoids some disadvantages of using Gaussian beams and improves the metallization efficiency.
- Metallization in an argon environment can avoid oxidation of the formed aluminum layer. Argon can dilute the nitrogen generated by the decomposition of aluminum nitride, weaken the high-temperature secondary reaction between aluminum and nitrogen, and improve the conductivity of the aluminum layer.
Be-cu aluminum machining china prototype company service include : aluminum cnc turning, aluminum milling service, aluminum extrusions, 5 axis machining aluminum, swiss machining aluminum, aluminum guide,aluminum products