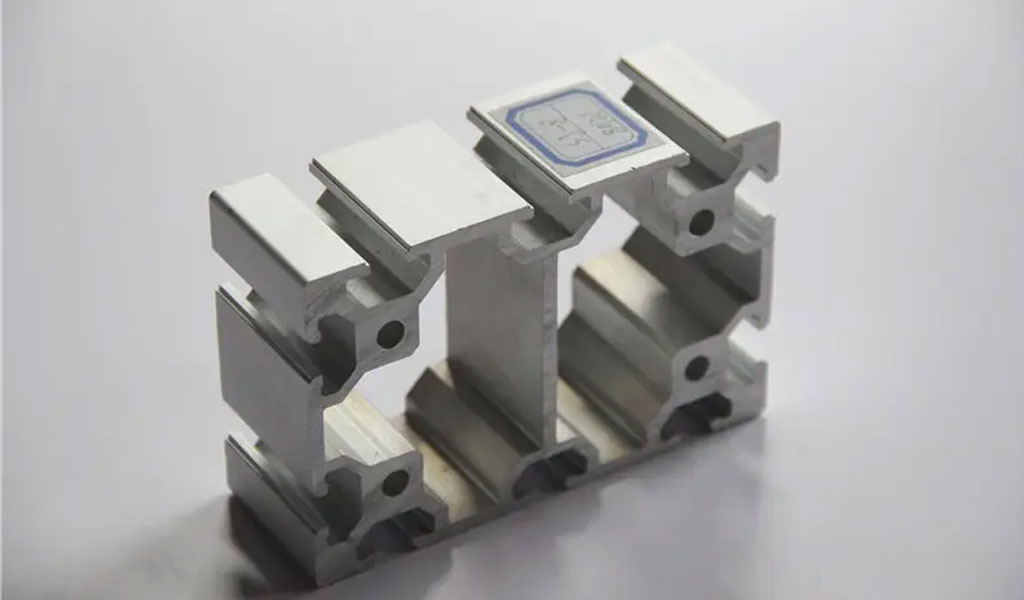
1. Hot Extrusion
It is widely used in the production of pipes and profiles of non-ferrous metals such as aluminum and copper, and belongs to the scope of metallurgical industry. Hot extrusion of steel is used both to produce special pipes and profiles, as well as to produce carbon and alloy steel parts that are difficult to form by cold or warm extrusion, both solid and bored (through-hole or non-through-hole). The dimensional accuracy and surface finish of hot extrusions are better than those of hot die forgings, but the mating parts generally still need to be finished or cut.2. Cold Extrusion
It was originally only used to produce pipes and profiles of lead, zinc, tin, aluminum, copper, etc., as well as toothpaste hoses (lead coated with tin outside), dry battery cases (zinc), bullet casings (copper) and other parts. In the middle of the 20th century, cold extrusion technology began to be used for carbon structural steel and alloy structural steel parts, and was later used to extrude some high carbon steel, rolling bearing steel and stainless steel parts. Cold extrusions have high precision and smooth surfaces, and can be used directly as parts without cutting or other finishing. Cold extrusion is easy to operate and suitable for small parts produced in large quantities (the diameter of steel extrusions is generally not more than 100 mm).3. Warm Extrusion
It is an intermediate process between cold extrusion and hot extrusion, and the advantages of both can be achieved by using warm extrusion under appropriate circumstances. However, warm extrusion requires heating the blank and preheating the mold, high temperature lubrication is not ideal, and the mold life is short, so it is not widely used.Comparison Of Cold Extrusion And Warm Extrusion
Although cold extrusion has many advantages, the large deformation resistance limits the size of the parts, and also limits the cold extrusion process for materials with high deformation resistance. Although the hot extrusion forming method can reduce the deformation resistance of the material, due to heating, problems such as oxidation, decarburization and thermal expansion, the dimensional accuracy and surface quality of the product are reduced, so a large amount of cutting is generally required. as the final product. Warm extrusion is to heat the blank to an appropriate temperature below the recrystallization temperature of the metal for extrusion. Due to the heating of the metal, the deformation resistance of the blank is reduced. The forming is easy, the tonnage of the press can also be reduced, and the life of the mold is extended. However, unlike hot extrusion, because of heating in the low temperature range, the possibility of oxidation and decarburization is small, and the mechanical properties of the product are not much different from those of cold extrusion. In particular, materials that are difficult to process at room temperature, such as stainless steel with precipitation hardening phase, high carbon steel, some steels with high chromium content, high temperature alloys, etc., may become machinable or easy to process during warm extrusion. Warm extrusion is not only suitable for difficult-to-process materials with high deformation resistance, but also for low-carbon steel suitable for cold extrusion, because warm extrusion has the advantage of facilitating continuous production. During cold extrusion, including cold extrusion low carbon steel, pre-softening annealing is generally performed before machining, and annealing treatment is also performed between each cold extrusion process. Passivation treatment is carried out before cold extrusion. This makes it difficult to organize continuous production. During warm extrusion, pre-softening annealing and annealing between each process may not be performed, or surface treatment may not be performed, which makes it possible to organize continuous production. At least many auxiliary processes can be reduced* Warm extrusion can use a large amount of deformation, so that the number of processes can be reduced. Die costs can also be greatly reduced, and high-rigid high-priced forging equipment can be used, and general-purpose forging equipment can be used. Therefore, although warm extrusion needs to heat the metal, the total machining cost is still relatively cheap. When complex non-axisymmetric special-shaped parts, warm extrusion can play its role.How to determine the optimal die temperature for warm extrusion
During warm extrusion, the heat transfer from the warm billet and the work done to overcome the friction between the billet and the die heat the die. Elevated die temperature may cause changes in die strength. In addition, the combination of cyclical changes in temperature and cyclical changes in extrusion pressure increases the likelihood of fatigue failure of die materials. Changes in mold temperature during production can also cause undesired phenomena in the product: for example, the product size will change with the increase in the amount of production; the reduction of the lubrication effect will cause scars on the surface of the product; and some areas of the product may have tops. Unexpected microstructure. Therefore, it should be clear about the temperature of the mold and the product when it is formed. There are two important issues: First. To determine the area with the highest temperature on the mold; secondly, in order to maximize the life of the mold, the optimal mold temperature during warm extrusion should be determined. This temperature may be related to tempering stability, tensile strength and fatigue strength. This paper presents on the one hand the results of a strength study of tool steels and their use to accurately estimate the optimum temperature for warm extrusion dies, and on the other hand some measures to maintain this temperature during production. The degree of die heating depends on many factors, such as the preheating temperature of the billet and the die, the size of the billet, the contact time between the billet and the die, the total time of an extrusion cycle, the number of cycles, die design, and heat transfer conditions (coefficients), etc. Temperature changes in the mold are limited to a relatively thin layer of material on the mold surface. There is no change in temperature at a depth of a few millimeters from the surface of the mold. The temperature distribution in the rest of the mold is constant and related to the average value of the heat flow. The first cycle of extrusion is usually the most dangerous due to the considerable temperature change, resulting in high thermal stress. As the number of extrusions increases, the temperature change will decrease until thermal equilibrium is achieved. This temperature steady state for any cycle can be characterized by the average contact temperature, the maximum temperature, or the equivalent temperature that causes the same microstructural change in the tool steel when the temperature is varied within a certain range. The equivalent temperature can be indirectly determined by measuring the microhardness on the cross section of the mold after a certain number of products have been produced. Assuming that the maximum equivalent temperature on the inner surface of the mold that is etched with the preheated billet is known, it is possible to perform some required tests on the strength of the tool steel under constant temperature conditions equal to the equivalent temperature.Be-cu aluminum machining china prototype company service include : aluminum cnc turning, aluminum milling service, aluminum extrusions, 5 axis machining aluminum, swiss machining aluminum, aluminum guide,aluminum products