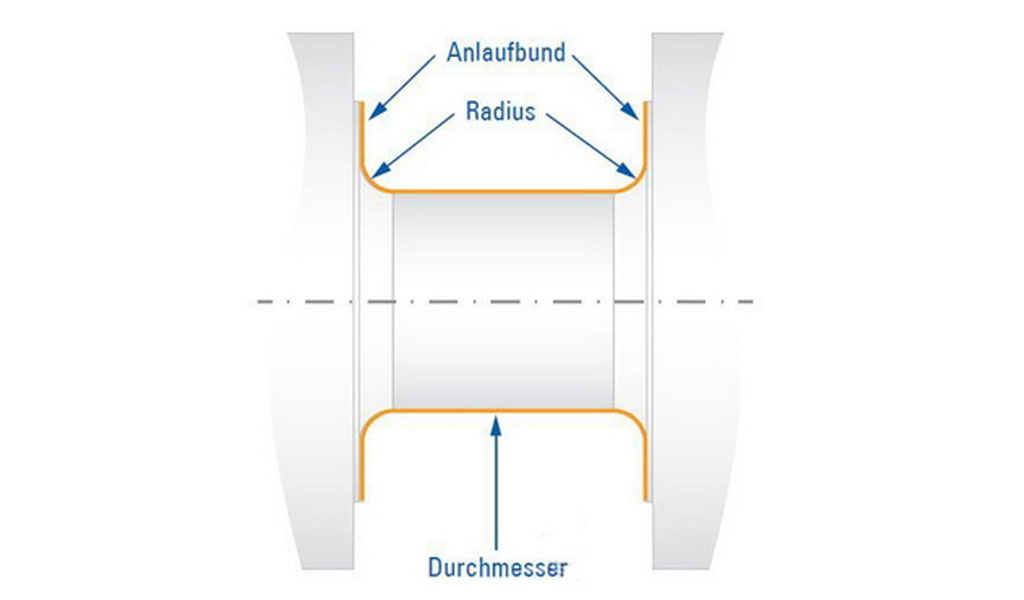
Rigorous Crankshaft Grinding Machining Details Use vector grinding to machine flanges, radii and diameters in one tight machining step.
Take the truck crankshaft as an example
Crankshaft cnc machining is a good example of this challenge. The efficiency and stability of the entire engine depend on this core component. Therefore, all kinds of bearings need to be finely machined by a grinding process, and the precision must reach the micron requirement. Especially in truck production, the technology used has to be subject to demanding requirements, such as truck crankshafts that always have to have a very high stability due to the long operating times of their engines. Therefore, when grinding such crankshafts, fine machining is required, not only for the end faces of the connecting rod and main journals, but also for the fillet (radius) between the bearing surface and the flange. Every corner of the core assembly of the entire engine needs to be carefully machined to become a perfect workpiece. Minimizing vibration for smooth operation is a must for truck engines, and it is this particular quality requirement that makes it a pattern that automakers are following. Some cars made by German manufacturers already have crankshafts machined in a similar way. The combined grinding of its bearing surface and radius is particularly challenging. On the one hand, the internal stresses generated by the machining of the part can cause changes in the dimensions of the part. This is why the time-consuming preliminary grinding step is followed by precision grinding. On the other hand, the technology currently used involves a lot of wheel wear. The transition from fillets to flat collars places particular stress on the tool. All in all, the combined grinding of bearing surfaces and radii is not only particularly expensive but also time-consuming and labor-intensive.Compliance with various grinding requirements
The head of the Grinding Technology Department of a company in Germany explained the beginning: “In view of all this, our technology for vector grinding – a development based on the complex processes and various technologies used so far The new technology has been thoroughly analyzed. Using this technology, the machining speed of the spindle and connecting rod bearings, which are difficult to perform grinding work, has become faster, and therefore, the cost has been reduced even more.” This project of the engineers The development stems from a simple observation: Grinding the cylinder diameter and machining the flat flange on the crankshaft have completely different requirements. While the center diameter is given a perfect, parallel surface through a multi-stage machining process (from roughing to finishing, to fine machining and polishing), the slightly rougher flanges require significantly fewer machining steps. The part deforms in a specific way during machining, making the situation even more tricky for mechanical engineers. During diameter machining, radial bending occurs. Therefore, power reduction is required when performing such machining. The axial bending during the machining of the flat flange is negligible. However, this poor contact condition has a tendency to cause overheating, which can wear the grinding wheel fasterThe key to success: precise control
“Given all these differences, you might especially want to strictly separate the grinding of the diameter and the flange, for example, so that the grinding speed can be adjusted correctly. Of course, this slows down the process. Instead, Our vector grinding technology can be combined in a single all-encompassing, complex prototype machining process. We control the grinding speed and the motion of each axis separately, and each subroutine is precisely controlled,” said the person in charge. The end result shows its unique advantages: This new technology enables the initial grinding of connecting rod bearings, main journals and sleeve separable bearings, approximately approx. Save a third of your time. As a result, a crankshaft with seven bearings can be fully ground in 20 minutes (instead of the previous 35 minutes), a major advance in mass-producing crankshafts, ultimately resulting in a significant reduction in the cost of components. In addition to this, precise process control is a guarantee of lower tool costs, as diameters are usually machined at lower power at the beginning of the process in order to reduce the impact on the grinding wheel. The principal confirms the huge cost advantage: “We expect this to cut tool wear by a third per component.”Technology for the future
Since the beginning of this year, the German company has applied the technology to vector grinding machines. The first products are currently in truck production. However, there is no obstacle to a broad expansion of car production. The person in charge said: “The current trend is moving towards the application of our technology, so to speak, because the miniaturization of car engines means that ultimately more forces are applied to the crankshaft. Therefore, more and more components are used. Extensive grinding will be a must. With vector grinding, we have today a more efficient technology.” For such a competitive advantage, the engineers also intend to apply it to their zero parts are being processed. For example, both camshaft and gear shaft machining benefit from vector grinding in a similar way. “We believe that each situation has many application possibilities.” The person in charge said with confidence.Be-cu aluminum machining china prototype company service include : aluminum cnc turning, aluminum milling service, aluminum extrusions, 5 axis machining aluminum, swiss machining aluminum, aluminum guide,aluminum products